Turbine failure is expensive, time consuming and should be avoided at all costs! Three of the most common failure modes are erosion, fatigue, and cavitation. This article explains what they are and the hydropower maintenance you can do to avoid them!
What is erosion?
Erosion is caused by small particles of debris passing through the turbine system. The fast movement of the particles can deform metal surfaces. Over time, when this process is repeated, material is removed, and the surface of parts becomes worn. The amount of erosion depends on a number of factors: the quantity of debris, the type of debris, turbine material and the location of the part [1]. Often the worst erosion occurs on high head turbines like Peltons. Where the water is moving very quickly through the spear valve, erosion can result in tracks being cut into the surface of the spear. This changes how smoothly the water flows leading to reduced power output from the turbine. In all turbines, over time the repeating contact between silt, sand and small stones with metal surface will lead to wear.
What is fatigue?
Fatigue occurs when a part is loaded repeatedly. This stresses the microstructure, like when you snap a paperclip by bending it backwards and forwards – small cracks begin to form, and the repeating load will cause the crack to grow [2]. In hydro-turbines, many of the rotating parts experience repeated loadings. For example, a single bucket in a Pelton turbine experiences a greater load when it is being hit by the water jet. If a crack grows, the part may fail slowly. Alternatively, the crack may make the part more likely to fail suddenly. Either way, failure of turbine parts as a result of fatigue will significantly increase your hydropower maintenance costs.
What is cavitation?
When water passes through a turbine, its pressure and velocity changes. At a microscopic level, tiny bubbles in the flow of water experience these same changes. When these bubbles burst on the surface of components, they can cause tiny holes to form in the material [2]. Similar to both erosion and fatigue, as this process is repeated, the wear can become worse and worse. In extreme cases, cavitation can eat right through a turbine blade! Cavitation tends to affect reaction turbines (like Francis and Kaplan) the most as they experience big changes in pressure. However, it can also be very damaging to Pelton buckets and Crossflow blades too.
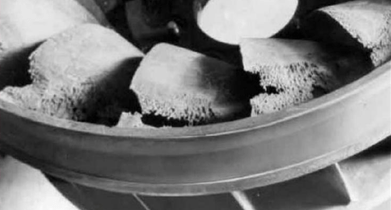
Figure 1 – Cavitation damage on the blades of a Francis turbine [3].
- The best way to combat all of these types of failure is to be aware of them. Inspect components regularly and make note of any apparent signs of wear. Look out for pitting (small holes), cracks and notches forming on the surface of key components. Knowing about problems early on can help to keep down the operating cost of hydroelectricity. If it is difficult to access some components, Hydro Maintain can arrange for inspection of your turbine using specialist equipment.
- Make sure civil structures are doing their job. Try to prevent as much debris, particularly silt and sand, passing through the turbine. If there is a de-silting bay, be sure to flush it out regularly. Erosion affects how much power your turbine can generate but it could make fatigue even worse. A hydropower maintenance visit from Hydro Maintain can ensure that your civil systems are doing what they are supposed to and are being properly
- Heat treatments and coatings can be used to improve resistance to surface deformation. If installing or overhauling a turbine runner in a location with very high silt content, it may be worth considering a specialist finish on the runner. These can prolong the lifetime of the runner by resisting erosion. Contact Hydro Maintain if you would like to know more.
Hopefully it will never happen, but it is good to know about the ways that your turbine could fail! If you need help diagnosing a fault with your hydropower equipment or want to find out more about our hydro maintenance services, don’t hesitate to contact Hydro Maintain today!
References
[1] Chitrakar, Sailesh, Hari Prasad Neopane, and Ole Gunnar Dahlhaug. “A review on sediment erosion challenges in hydraulic turbines.” Sedimentation Engineering (2018): 9. [2] Dorji, Ugyen, and Reza Ghomashchi. “Hydro turbine failure mechanisms: An overview.” Engineering Failure Analysis 44 (2014): 136-147. [3] https://www.researchgate.net/figure/Cavitation-damage-on-the-blades-at-the-discharge-from-a-Francis-turbine_fig94_36721047